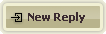 |
|
12-13-2009, 04:41 PM
|
#141
|
Senior Member
Join Date: Apr 2006
Posts: 625
|
.....I HAVE ENOUGH PROBLEMS WITH A CELL GUESS I'LL SKIP THE ISSUE OF WI-FI .....I SOLVED THE PROBLEM OF TV WITH THE USE OF A VIDEO DISC PLAYER....MIGHT HAVE AN ISSUE WITH COMPUTERS THAT IS JUST TOO MUCH FOR ME TO DEAL WITH AND HAVE TO GO TO RADIO SHACK FOR GUIDANCE.......geofkaye and the Rivercity Girlz....
__________________
|
|
|
12-14-2009, 07:10 PM
|
#142
|
Senior Member
Join Date: Apr 2009
Posts: 212
|
A Brief Aside
Many years ago I had cable TV but didn’t like it. It was basically the same as broadcast TV with a couple of movie channels and some infomercials. It also cost me a substantial monthly fee which felt like a waste. For the last 20 years here in the bay area I put up a TV antenna wherever I lived and received plenty of channels for free. More recently, with the conversion to digital TV the number of channels has effectively doubled, and that’s just counting the ones in English. I never wanted, or felt the need for satellite or cable in all those years, especially at $40 to $60 per month, though I will admit that some programs and series are more and more available only on satellite or cable.
I see many RV’s around with the large dome satellite dishes. Their owners seem rather wealthy and retired in most cases, so perhaps they don’t care about the monthly fees, not to mention the expense of installing the equipment. It seems to work well, at least as well as satellite does most anywhere. The picture quality is quite good, but it still seems to suffer from the “150 channels and nothing on” scenario.
Many years ago I bought my young son a PS1, (Sony Play Station 1), which later became a PS2, and now a PS3. For most of those years they were just gaming stations, and well worth the money for the many hours of entertainment my son enjoyed. I was never into gaming myself, but with the PS3 it became possible to download movies over the internet. The PS3 has Wi-Fi built in, so I added a wireless router to my PC and was ready to go. For about $4.00 I could download a typical movie in standard definition and then watch whatever I wanted. It would take 4 to 6 hours to download with my not so speedy DSL connection, but it was fine. I don’t watch that many movies, and I don’t mind paying for what I actually use, but I don’t like monthly fees.
More recently Netflix got together with Sony and offered a fair portion of their movie library for “movies on demand” through the PS3. They are also available direct to your computer, and now days more and more people are dedicating a PC to their entertainment center, meaning there is now more than one way to watch internet movies on the TV in your living room. When I say, “movies on demand” I mean you pick the movie you want to see and just start watching it. When I say movies I mean TV Series, and all kinds of stuff, not just full length movies.
I still don’t like monthly fees, but for $9.82 per month, including tax, they finally hit my price point. It’s not all perfect. There are some compression artifacts. I have to laugh when first officer Spock’s black hair floats above his head for the blink of an eye when he steps down to the bridge. Mostly it’s very watchable though, and way better than the old analogue days when we watched through snow, crawling ants, and colored shadows.
What I really like is sitting down to watch an hour long TV show and skipping all the commercials. Let me be clear, I don’t skip over the commercials, they just aren’t there. 30 to 45 minutes of TV is perfect with a meal. I sometimes watch a movie in two parts, half with one meal, and half a day later, or whenever I want, because I can. I am no longer tied to their schedule, and if I don’t like the show it costs me nothing to turn it off or find something better.
Not all movies are available via Netflix, and not all of those are available to be viewed instantly. Thousands are, but many more are not. I expect that many more will be available over time, but I can also see where the cable, satellite, and commercial sponsors have got to hate this, and will probably do their best to kill it. There is also the movies by mail option, but that doesn’t work so well for an RV on the road.
All this relates to my Stealth Camper design because I am working hard to have excellent Wi-Fi capability, but not even interested in Satelite. Even if there weren’t movies on demand over the internet I would do the same. The internet is my lifeline to communicate with all of you and many others. I figure that between the internet and broadcast TV for things like local news, I have everything I need.
I think the golden age of satellite and cable are almost over. I say “golden” for the big money made by the satellite and cable providers. I imagine that they will adapt, and you can be sure they will be hitting up your congressman to protect their interests, but the writing is on the wall. Data is data, and economies of scale will drive the cost of data delivery ever lower.
To be continued…
__________________
|
|
|
12-23-2009, 06:35 PM
|
#143
|
Senior Member
Join Date: Apr 2009
Posts: 212
|
Odds and Ends
It’s cold and rainy now, so I keep working on the little things I can do indoors. Progress seems slow to nonexistent, but the hours keep melting away.
I spent most of a day making my overhead light out of X-mas light LED’s. The end result is that it works fine, makes about 40W of light relative to incandescent, and draws about 1.1A, which is about 13.2W at 12V. I made it from one of the two florescent recessed ceiling lights that came with the truck when I bought it. It was burned out, and not just the bulb, so I had to do something. By comparison, the other identical light, which still has the original florescent bulb, and still works, draws about 2.2A (26.4W), and puts out about 60W of light relative to incandescent. That makes my LED lamp about 33% more efficient. I must say, that is a lot of work to save just 1 amp. I needed to do something, since the light was broken, but I can’t claim that it was cost effective, or an efficient use of my time.
My LED light is also considerably more blue, or less “warm” than the fluorescent light. I anticipated that, and mixed in 25% red, yellow, or green LED’s to try and warm it up, but it wasn’t enough. It’s not objectionable or anything, but it’s easy to see the difference when the two lights are on side by side. By the way, red plus green makes yellow in the additive color system, and yellow is what you need to warm up blue. The human eye is most sensitive to color shades around white, so getting the white balance just right can be difficult.
I made a similar LED light array for the filter module above the stove with similar specifications. I also removed the AC fan that came in the unit and replaced it with a 12V squirrel cage blower. The original design was intended to vent up through the ceiling via an 8” diameter vent, but I don’t want any more holes in my roof. I rigged it to draw air in through the filters and then exhaust it back out the front and side in the general direction of the central overhead exhaust fan which is just a few feet away. I realize that it isn’t an ideal solution but I figure if I can catch some of the tiny floating grease droplets in the filters then there will be less to stick to every other surface. It will be interesting to see if the grease gums up the blower over time.
I needed about 5 other small task lights over work surfaces, the sink, countertops, the computer nook, etc. I was planning to make those out of LED’s as well, but then I found an ideal little single tube florescent light at the local hardware store. They are 12V with provisions for internal batteries, but also have a little socket for 12V input. They draw about an amp and put out about 30W (equivalent incandescent) light so they meet the need just fine. It remains to be seen how long they will last, and how much pounding they will take, but they were cheap so I figured, why not. I can always replace them later if I want.
I also wanted reading lights for the upper and lower bunks. I found some LED type low voltage lights intended for outdoor landscape use. They have a nice cast aluminum hood and a descent reflector that makes a nice cone of light for reading. I wanted all of my lights, including these, to have switches right at the light, so I had to modify them. In this case it was just a matter of drilling out the cast aluminum hood and wiring in a small toggle switch. I also needed a small base for wall mounting. Fortunately a plastic sprinkler head and a very short length of threaded plastic pipe make a nice sturdy mount. It can twist on the pipe threads for azimuth and the head clamps and pivots up and down for elevation so it is fully adjustable. These low voltage LED lights are made for 12V AC but they seem to work fine for 12V DC.
My last hole in the roof is for the toilet flue. I made a 4.5” tube with a mounting flange out of sheet aluminum. It will bolt to the roof to create the pipe up into the flue cap which is actually a small upside down roasting pan. The actual flue pipe is 4” and will slip up inside with a little fiberglass bat jammed in between and a bead of high temp silicon to finish it off. I modified a secondary ring to cover over the flange where it mounts to the roof and will fill the area under the ring with more high temp silicone.
I have been updating the photo gallery with pictures. You can look them up under keyword “Stealth”
To be continued…
|
|
|
12-24-2009, 06:57 PM
|
#144
|
Senior Member
Join Date: Jun 2008
Location: West Chester, Ohio
Posts: 483
|
They are starting to use LED lights in stage lighting. My lighting guy has said the same thing. They are very blue and unnatural. He calls them candy lights.
Doc Weaver
__________________
Doc Weaver '98 Freightliner FL60 pseudo toy hauler
|
|
|
12-26-2009, 05:58 PM
|
#145
|
Senior Member
Join Date: Apr 2006
Posts: 625
|
.....Got some new ambulance side lites that are LEDs and an getting 1 more at OEM cost.....retail is $350ea......all LEDs are the same it is the reflectors that are the difference and the color of the covering.....it is all in reflector science now not so much the LED diode ....the white lite is a thing of the past unless specified.....WELEN HAS A KILLER $800 LITE THAT I'M GETTING A SAMPLE...IT IS A SCENE LITE AND ALSO A FLOOD....AGAIN IT IS ALL REFELCTOR TECHNOLOGY....geofkaye and the Rivercity Girlz less 2 that were fired before Christmas....
|
|
|
01-05-2010, 07:11 PM
|
#146
|
Senior Member
Join Date: Apr 2009
Posts: 212
|
I Conduit (and so can you)
I have pretty much completed the installation of the electrical boxes and conduit. The next step is to pull the wires. I should mention that I used plastic “handy boxes” for most things. When building a wall inside of existing FRP with 1.5” x 1.5” studs and using ½” plywood, you need a box that is no more than 2” deep. Handy boxes are perfect at 2”. They are also readily available everywhere, made of sturdy grey plastic, and have 7/8” knockouts on 3 sides. They are a bit small, and only contain a single outlet, but they can be screwed directly to the FRP with self tapping screws so they can easily be placed anywhere.
I used ½” water tight flexible conduit for most everything, even the relatively straight runs. It has thinner walls than the rigid grey plastic ½” conduit which allows for a little more room to pull the wires through. It also bends easily around corners at any reasonable radius, which means you can keep the runs as short as reasonably possible. It also avoids the need for a lot of individual pieces, 90 degree bends, offset pieces, couplers, etc. and just generally makes life easier. The conduit fits nicely into the 7/8” holes in the boxes. I did not use any clamps or fasteners at the boxes, just ran the conduit through the holes and clamped it to the walls.
I did run a bead of “Amazing Goop” ( http://www.eclecticproducts.com/ag_adhesives.htm) around the joint where the conduit enters the boxes to seal the entrance and make a tough flexible joint. Goop is a great glue for things like this. It grabs onto shiny smooth plastic better than most things, but if you have to you can rip it apart and peel the glue off to fix a mistake. In this case I wasn’t really trying to make a watertight seal, but I did want to make sure that the conduit didn’t slide around or pull out of position when I was (will be) pulling the wires through. There will also be quite a bit of the canned spray foam injected around the conduit to fill spaces around the Max-R insulation panels, and I didn’t want it finding its way into the electrical boxes.
I don’t know if this technique is per code, or if there is even a code that applies to what I am doing. I am an electronics engineer, not an electrician. I will make things that work, and are hopefully safe, but I have no idea if they meet code (and I really don’t care).
Some of the corners I have to go around were a bit of a challenge. The bend from the wall to the ceiling was a little tight as the inner plywood box has sharp corners while the outer FRP box has aluminum extrusions that are somewhat in the way. One technique that opens up the radius when going around a 90 degree corner is to approach the corner on a 45 degree bias. In other words, you don’t go straight up the wall and straight across the ceiling. Instead you go up the wall at up to 45 degrees near the ceiling, and then you exit into the ceiling at 45 degrees as well. It’s hard to explain with words, so check out some of the pictures if you need an example. They are located as always under keyword “Stealth”. By using this technique you can open a 90 degree bend to about 130 degrees, which opens up the radius and makes the wires easier to pull through the conduit.
I did as much planning on paper as I could in an effort to avoid conduit crossing in the walls. The conduit is 7/8” diameter, so at the point of crossing it is 1 ¾” thick. Considering that the studs are only 1 ½” thick it won’t fit by ¼” of an inch. I experimented with notching the conduit slightly to make it fit, but ultimately I decided on a simpler method. I just run the conduit where it crosses and then afterwards heat it with a heat gun and smash it down a little. The conduit becomes a little oval at the point of crossing but each side only looses an 1/8” of an inch or less, so it’s not much.
You may note from the pictures that the walls are rather densely packed with conduit. I might have gone a bit overboard, but my thinking was to accommodate every wire I could think of, and a few that might never be used. I not only used conduit for the AC wiring, and the 12V DC wiring, but also for things like antenna wires, to the TV’s and computers, Ethernet wires between the computer and the PS3, video and audio wires between the PS3 and the TV’s, and USB wires between the computer and the Wi-Fi amplifier. It may well turn out that I forgot something, and it will have to be tacked along the wall on the inside, but at least I tried.
All that conduit will negatively impact the R value of the insulation in my walls. It will also mean that I have to cut lots of little oddly shaped pieces of R-MAX insulation to fit around it. That, and I already mentioned the canned foam to fill in all the gaps that will be created. It’s going to be tedious installing the insulation when the time comes, and I am sure I will end up wasting a bit in the process. The ceiling insulation, on the other hand, is 4 ½” to 5 1/2” thick so the loss of R value there should not be significant. Also the right side wall has more insulation as an unintended consequence of the side doors which became awnings so insulation and crossing conduit on that side is no problem.
Running conduit through the studs required lots of drilling, but nothing difficult, just a standard 7/8” spade bit. Some of the electrical boxes required additional holes not supported by existing knockouts. A 7/8” hole saw made quick work of those. You do need to be a bit careful though. That hole saw will grab into plastic and like to rip your hand off if you aren’t careful.
To be continued…
|
|
|
01-05-2010, 08:46 PM
|
#147
|
Senior Member
Join Date: Apr 2006
Posts: 625
|
.....huummm....never considered flexible conduit like the weather tight stuff.....huummmm.....great idea there Ran D. .....there is some that available that is not as large as 7/8 but i can't remember where it is right now.....anyway great Idea!......geofkaye and the Rivercity Group less 2.........
|
|
|
01-06-2010, 06:24 AM
|
#148
|
Senior Member
Join Date: Jun 2008
Location: West Chester, Ohio
Posts: 483
|
I used "liquid tight" on my truck. It's much easier to work with than stiff conduit. We use it in our church AV installs as well. If it doesn't need to be waterproof, Parts Expresshas all sorts of wire loom. We use that too.
Doc Weaver
__________________
Doc Weaver '98 Freightliner FL60 pseudo toy hauler
|
|
|
01-16-2010, 09:14 PM
|
#149
|
Senior Member
Join Date: Apr 2009
Posts: 212
|
400 Pounds of Electrons
I now have 6 each 6V batteries, for a total of about 400 pounds. These are top of the line AGM (Absorbent Glass Mat) batteries from Lifeline, GPM-4CT, for a total of about $1,500 with shipping and tax. They had to put them on a pallet and ship them freight but I am starting to get used to that where this project is concerned.
This means I have now made my last big ticket purchase. With the exception of the catalytic heater, which I had to send back because I ordered the wrong one, I have all the big ticket items in my possession now. My house is full of stuff that doesn’t belong, like a toilet in the kitchen, and a range in the living room. I am really hoping that my monthly cash flow will turn positive now. Unfortunately, as Blizz will attest, you can spend lots of money on the little things as well.
I went on line with McMaster Carr and found most of what I needed for battery cables pre-made.
http://www.mcmaster.com/#battery-terminals/=590gck
It’s not cheap, but it’s probably a lot easier than making your own. They have cables for paralleling up to 3 batteries, which is what I needed, and they also have cables for connecting the batteries in series. It’s handy that these cables seem to come in just the right lengths which is probably because at 66 pounds each, the batteries I used are about the same size as heavy duty truck starter batteries, so they connect together quite similarly.
The lugs on these pre-made cables are cast right onto the wire out of lead. Lead is fairly soft but the lugs are so thick that they seem to be plenty strong. The pliability of the lead probably also insures that it conforms to the mating surface with plenty of contact area. I haven’t noticed any heating even with high currents running through them, so they must be working well enough.
I did buy some 2/0 welding cable and solder on connectors for the link from the battery bay to the Inverter bay. I found them here:
http://www.mcmaster.com/#catalog/115/781/=590ep3
My experience with the solder on connectors is quite good so far. They were easily soldered on with a propane torch. Just strip the wire, push it into the connector, and heat the connector until the internal solder slug melts. Gentle pressure on the wire will force it into the molten solder and flux making a very strong joint. The solder did not wick up the wire much, so it remained flexible right up to the lug. Depending on the orientation of the lug, some excess solder may drip out, so put something down to catch it. Since the solder joint is up inside the lug, there is no way to inspect it visually. I did a bit of a pull and wiggle test and it seemed very solid though. I also found no heating at the lug even with very large currents running though it, so the implication is that it is a good electrical joint.
These solder on connectors aren’t cheap, but for just 4 lugs like this project, they are a lot cheaper than buying a large crimping tool for use with the crimp on lugs. If you already have a crimping tool, or can borrow one, the crimped lugs are probably cheaper.
The battery tray I am using is just 1/8” steel, about 22” by 22” and 1.5” deep. It fits the 6 batteries perfectly, which is dumb luck because it came with the truck as a slide in tool shelf. I removed the slides as I don’t think they are strong enough to carry the weight. I also put 6 lag bolts up through the top of the battery box into the wooden floor boards of the living quarters. The battery box is already welded to the steel floor joists, but at 400 pounds I wanted some insurance.
I thought long and hard about how to mount the batteries. I wanted them to be somewhat shock mounted to reduce the pounding. I was considering rubber vibration dampers, like motor mounts, but in the end I decided to keep it simple. I set the tray full of batteries on top of one inch of EPP (Expanded Polypropylene) foam with more of the same along the back, sides, and front, set within the door frame. I welded some D rings into the side walls of the box for heavy nylon straps across the top and another across the front to make sure they stay in the battery box.
I wanted to have some sort of a fuse or circuit breaker for the batteries, but I calculate the maximum required current from the batteries at close to 250A. I didn’t find any circuit breakers or fuses in that range at the local home improvement store. They might be available somewhere, but I wanted this design to be serviceable using readily available parts when possible.
High current circuit breakers can be very expensive. I also think it is dangerous to use a circuit breaker that was designed for AC in a DC circuit. An AC circuit has a zero crossing, or a point in time when the voltage is zero, every 8.3 milliseconds, which is an opportunity for any arc caused by the opening of a switch to extinguish. DC has no zero crossing and can sustain an arc indefinitely. You might not think 12V is much to worry about arcing, but once the arc is established, and the air ionized, it will conduct relatively low voltage over a considerable distance. If the electrical contacts aren’t far enough apart, or there aren’t other provisions to extinguish the arc, the circuit breaker can arc until it melts or starts a fire.
I ended up using standard 100A cartridge fuses. They are only about $7 each which is nice. The connection between the two series batteries was an easy place to mount them, so that’s what I did. With 3 sets of two batteries in parallel, each fused for 100A, that’s 300A total, which is a reasonable margin above the 250A that the inverter might require.
A fuse is really just a piece of wire that gets hot and melts when there is too much current though it. The alloy and thickness of the wire is chosen carefully to give the desired characteristics. When the circuit opens, it is just like opening a switch, so an arc will be formed. I opened up one of these cartridge fuses, and the fuse wire itself is surrounded by a white power, probably baking soda or similar. As the molten metal of the fuse wire drips away, the powder will fall into the gap and extinguish the arc. It’s simple, but clever. I have no concerns about using fuses in a DC circuit.
A different concern is what will happen if I use my house batteries to “jump” the starter battery. Depending on the total resistance of the circuit the surge current could easily blow my fuses. I don’t intend to jump my starter batter hardly ever, so it will remain a concern for another day. A dead starter battery and a dead house battery (due to blown fuses) would really suck though.
I might also connect my house batteries to my starter batteries to charge them all in parallel from the alternator while on an extended trip. In that case all the various batteries would be reasonably charged to begin with, so the surge current when connecting them should be more reasonable, and hopefully not nearly enough to blow my fuses.
One other concern is that one of my 3 sets of parallel batteries might try to provide all the current required by my inverter, in which case 250A could easily blow the fuse. In practice the batteries are all brand new and very well matched so they share the current almost equally. Eventually, as the batteries ware out, they will become more imbalanced, and this will be more of an issue. I will have to monitor their health from time to time. If they ever do get too far out of balance, and it can’t be cured by an equalization charge (controlled overcharging) then the batteries will have to be replaced, because replacing one battery out of a set of worn out batteries is just inviting trouble.
To be Continued….
?
|
|
|
02-02-2010, 06:50 PM
|
#150
|
Senior Member
Join Date: Apr 2009
Posts: 212
|
I Was Wrong (Again)
I was doing some testing on my electrical system. It was pretty much my first chance to do so with everything in place. I tried various AC loads up to about 2,300W, which is getting close to the limit of my inverter (2,500W) and everything was working as expected. As a result of the testing I had managed to draw my batteries down a bit and my Battery Charger was pumping its full rated 90A from shore power. I decided to try my Honda Eu2000i generator instead and it fired up happily and was pumping 9.5A at 124VAC into the charger, so all was well. As I continued to try stuff the batteries were coming back up to 90% charge and I happened to apply a smaller AC load, something like 1,500W. My light plugged into the inverter started flickering, and my generator ramped up to full throttle for a couple of seconds before giving up and cutting its AC output.
My first reaction was, Oh crap, followed immediately by, what the hell? My generator is happy with a heavy load, but doesn’t like a light one? The flickering light was my best clue. I remember back about 6 months ago when I did my first testing with the inverter and the Power Supply (Battery Charger) but no batteries. I noticed the flickering then and assumed that it was because I didn’t have any batteries to stabilize the DC side of things. I now have about 400 pounds of batteries so that is no longer an issue. I also remembered that the flickering went away when I unplugged the little module that converts my Power Supply into a 3 stage battery charger. I unplugged the module again, and sure enough everything started working as expected.
It seems my battery charger was hunting, trying to decide whether it should be in Float, Absorption, or Bulk mode (I don’t know exactly which). This was pushing the DC voltage at the batteries up and down slightly which was in turn causing the flicker at the inverter output. It was also flickering the current draw from my generator, which really pissed it off.
When my batteries were more depleted, the battery charger wasn’t confused about what stage it should be in. It was happy to stay in bulk mode, and just push 90A. This made the inverter and generator happy as well. Even as the batteries came up to full charge, a really heavy load was enough to convince the battery charger to remain in Bulk mode, so everyone was happy. It was only when the batteries were more fully charged and the load was reduced that the charger wasn’t sure what to do.
Without the module my power supply is still a battery charger, but it only has one stage, “float”. In this case, float means that it will try to bring the batteries up to 13.56V, and will give them all the current they will take at that voltage, up to a maximum of 90A. If the batteries will take the full 90A then the voltage has to drop to whatever the battery voltage is with 90A input. Depending on the battery state of charge, that will be between 11V and 13.56V. To put all this another way, my battery charger is really a 13.56V power supply with a 90A current limit.
With the module installed my battery charger has 3 stages:
Bulk 14.67V at up to 90A
Absorption 14.16V at up to 90A
Float 13.56V at up to 90A
All three stages work the same way. They put out the specified voltage unless limited by the 90A current limit. The idea is that you can safely charge a heavily discharged battery at a higher current, which means you can safely push that higher current with a higher voltage. As the battery approaches full charge you need to back off the voltage to avoid overcharging the batteries which would shorten their life.
This is all a fine idea, and well proven, but it really doesn’t apply to my situation. I have a large number of high quality AGM (Absorbent Glass Mat) batteries. If I were to run them down to say 50% charge, and then hit them with a bulk charge voltage of 14.67V and no current limit, they would probably happily accept 600A or more. This would indeed be the most time efficient way to charge my batteries, but I simply don’t have that kind of power available. My generator isn’t powerful enough, and my battery charger is intentionally sized so as not to overload my generator.
In my case it doesn’t matter if the battery charger is trying to push 13.56V, or 14.16V, or 14.67V, the current is going to be limited to 90A. As the batteries come up to full charge there will eventually be a point at around 90% of charge, where the 90A limit will no longer apply. At this point my charger should be in Float stage anyway, and limiting the voltage to 13.56V. As it turns out, I don’t need a 3 stage charger. A one stage or a 3 stage charger will both do almost exactly the same thing, and charge my batteries equally quickly.
So, I was wrong about needing a 3 stage battery charger, and I wasted $29 on that module. As mistakes go, this was a cheap one…
It turns out that I was also at least partly wrong about one other thing. I designed my truck so the generator would drive the battery charger and only the battery charger. The idea was that any sudden increase in load would be provided by the batteries so the generator would never see a sharp increase or decrease. This would allow me to run the generator in ECO mode where it throttles down to provide only the power that is needed.
My plan works perfectly so long as the batteries are below about 90% of charge. In that case the battery charger is pumping the full 90A which means the generator is happily pumping about 80% of its rated capacity, and all is well. If, however, the battery is nearly fully charged, then the battery charger isn’t charging much and the load on the generator is very small. In that case, a sudden increase in load, like turning on the air conditioner, is transmitted almost immediately all the way back to the generator. Fortunately, even in ECO mode at full idle, the generator seems to ramp up quickly enough to avoid anything bad happening. The batteries are probably taking the edge off the surge, and both the generator and the battery charger are willing to deal with low voltage for a second or two until everything has a chance to stabilize. It’s not ideal, but so far it all seems to be acceptable.
To be continued….
|
|
|
02-03-2010, 06:34 AM
|
#151
|
Senior Member
Join Date: Feb 2009
Location: St. Paul, MN
Posts: 1,819
|
Interesting reading Ran. WAY above my head, I understand very little of it. But I like reading it.
__________________
'03 Freightliner FL112, 295" wheel base, with '03 United Specialties 26' living quarters, single screw, Cat C12 430 h/p 1650 torque, Eaton 10speed , 3.42 rear axle ratio
|
|
|
02-03-2010, 06:45 PM
|
#152
|
Senior Member
Join Date: Apr 2009
Posts: 212
|
Lets talk about protection…
Son, there’s a lot of fine ladies out there, oh wait, not that kind of protection. Circuit protection…
Now that I have my electrical system pretty much completed, I can walk through all the various protection features. It’s not at all like your house wiring. Your house probably brings the power in from the street, which then goes into your breaker box. You have a couple of big breakers or fuses on the mains, then a bunch of smaller breakers or fuses on each of the branch circuits. In the old days, that was pretty much it. More modern houses probably also have one or more GFI (Ground Fault Interrupter) in the bathroom and or kitchen. Your individual appliances will often have their own individual fuses or circuit breakers built in, but not always.
My truck is both more complex, and smaller. Let’s walk through the system from beginning to end and check out all the safety features. This is just my truck, which may be similar to your truck, or not. I am no certified electrician, so jump in if I am violating some code or standard practice. I designed everything with safety in mind, but I might have overlooked something.
If I am running off of shore power then the AC comes in through a watertight covered plug on the outside of the truck. It then goes to a socket inside the generator bay through a 15A fuse. The plug that feeds the battery charger, and only the battery charger, either plugs into this socket or into the generator.
The generator, a Honda EU2000i has a 20A button breaker on the front panel. It also has built in electronic protection circuitry that is reset by turning the motor off and then starting it up again. In practice, I have never popped the breaker, but I have tripped the electronics when the motor surges to meet a rapid change in demand. It is immediately obvious because the motor starts running happily as if under no load, which is exactly what it is doing.
The battery charger has 2 each 40A automotive type fuses which are intended to protect it from a reverse polarity connection to the battery., The DC output of the battery charger is protected electronically. Most modern power supplies have what is called “fold back” protection. If it detects a load that it can’t drive, the output voltage will “fold back” to zero or near zero, or in other words, it will give up. Depending on the supply, it will try again briefly every few seconds and if the load is back to normal it will begin working normally again. Some supplies have to be power cycled to reset the fold back circuitry.
A battery charger is more complex than a simple power supply because the voltage has to give to match the battery voltage. Put another way, it regulates current not voltage, depending on the battery state of charge. Regardless, it can detect if the voltage and current are outside of acceptable ranges and shut itself down if it needs to. Likewise it can shut itself down if it gets too hot. None of this should damage anything, but abusing anything will kill it eventually.
The batteries have 3 each 100A fuses in series with each of battery pairs. (6 each 6V batteries configured as 2S3P (2 in series and 3 in parallel). I went over those earlier.
The batteries feed the inverter which has a lot of intelligent protection circuitry built in. It will shut itself down if the battery voltage is too low, or the battery input current is too high, or the AC load is too heavy, or it gets too hot, etc. All of this electronic protection is great, but designers always worry that it will fail, so they tend to use something like a fuse or a breaker as a back up. The inverter has a 15A breaker on each of its two banks of two output sockets. You can also hardwire into a single output for the full 30A. It’s only rated for 2500W continuous, so that’s a little less than 21A, but the short term surge current could be much higher, hence the need for the circuit breakers.
In my case the inverter feeds what amounts to two each 15A branch circuits. Since the inverter is already protected, there is no need for additional circuit breakers. I do run the branch circuits through a GFI though. A GFI serves a different purpose from a fuse or breaker. Fuses or breakers protect the wiring from overload, which could cause them to get hot and possibly start a fire. A GFI aims to protect the human using the power. It only takes a tiny amount of current to kill someone if that current should pass through their heart. A circuit breaker or fuse will not limit the current to anything close to a safe level.
The GFI measures the current in the hot (black) and neutral (white) wires and makes sure that they are equal and opposite. As long as they are, there is no stray current passing through some hapless human, so all is well. If you should put yourself between the black and white wires, you become the load, and the GFI won’t help you, but if you should manage to get between the black wire and ground, then the current going through you won’t be going back through the white wire like it should, and the GFI will shut the circuit down.
Many metal appliances have a ground wire (green) that connects to the outer chassis, which is the part you could possibly touch. The ground wire should never have any voltage on it, and should never have any current through it. Any current through the ground wire implies that something is wrong and will trip the GFI if you have one. Even if you don’t have a GFI, a dead short between the hot (black) and chassis (ground - green) will trip the breaker and hopefully save you that way.
Many plastic appliances have no ground wire, just hot (black) and neutral (white). They are “safe” because there is no way for you to touch the wires inside. Take them apart at your own risk.
My truck also has a 12V DC power distribution system. You might assume that 12V DC is inherently safe, but that’s not true. 12V will easily push enough current to kill you if it can get through your skin resistance. It’s true, you can grab the terminals of a 12V battery with both hands, and nothing will happen. Do not try it with wet hands though, and stay clear of any natural wet spots. The 12V batteries in my truck, be they the starter battery, or the house batteries, have tons of energy in them, more than enough to start a fire. Fuses or breakers are still necessary to protect the wires.
Beyond the link from the batteries to the inverter, which is protected by the 3 each 100A fuses, there is a 2nd link from the inverter to the DC distribution plate which is protected by a 60A circuit breaker. It is not a standard hardware store AC breaker though. It is made for DC use as well.
From there the current flows through 3 each 15A thermal breakers that feed the 3 DC branch circuits. These are mechanical devices that will break the circuit if the current gets too high, and will automatically reset themselves several seconds later when they cool down. If the short is still present they will open up again, and then close again, and then open again, you get the idea… They are convenient because you don’t have to run to the fuse box to manually reset them. They are not a total solution though, because they keep closing again. I also put 20A fuses inside the wall outlet boxes where the cigarette lighter sockets are mounted. If I blow one of those, then I have to remove 2 screws to remove the cover plate. The fuses themselves are the automotive blade type. They are convenient to use with matching crimp on lugs which are readily available at your local home improvement store.
To be continued….
|
|
|
02-06-2010, 04:22 PM
|
#153
|
Senior Member
Join Date: Apr 2009
Posts: 212
|
You can gage a man by his wiring…
Lets talk wire gage as it is used around the truck. I may have gone overboard in a few places, but at least I won’t have power robbing voltage drops everywhere.
All the wiring in my truck is stranded. I am told that solid wire would not stand up to the vibration. Speaking as the guy who has to make all the connections, stranded is more difficult to deal with, but I guess it is necessary.
All of the wiring, both DC and AC is a full loop, meaning both out to the load and back. I do not rely on the truck chassis to carry any ground return currents. There are some ground return currents related to the original truck wiring, tail lights, turn signals, marker lights, things like that, but nothing related to the house wiring.
The battery to the inverter uses about a 4ft loop of 2/0 (spoken “double aught” where aught is pronounced like “not” without the “n”). It’s very heavy stuff, and expensive too, but it handles lots of current. I measured only 94mV drop at 141A. That’s less than 0.1V for the milli-challenged.
My house batteries connect to my starter batteries through a heavy duty (250A) switch and about a 7 foot loop of 1/0 (single aught) wire. 1/0 is still very heavy wire, though not as heavy as 2/0, about the same size as the wire from the starter batteries to the truck starter motor. If I ever need to “jump” the truck from the house batteries it should have plenty of punch to get her started.
The 2 foot loop from the battery charger to the inverter carries up to 90A and looks to be about 1 AWG (American Wire Gauge). I don’t really know for sure as I just used the wire that came with the power supply.
I used 8 AWG for the 3 foot loop from the inverter up to the DC distribution bus. 8AWG is rated for 73A over short runs, and it has a 60A breaker in line, so it should be OK. In practice I expect it will never see more than 20A.
The 3 each DC branch circuits that carry 12V throughout the truck are wired with 12 AWG dual conductor wire that is sold for low voltage outdoor lighting. It looks like lamp chord, with a seam down the middle that can be split. It was a little easier pushing a single pair of wire through the conduit though I am sure I could have made individual wires work. The insulation on the wire is tough and overall it was pretty cheap. The disadvantage is that it isn’t color coded. It has a ribbed conductor and a smooth conductor, just like lamp chord. In my case I decided to make Ribbed = Red = 12V, and smooth or Blank = Black = Ground. The thick insulation does make it tough to stuff into a small handi-box with a cigarette lighter socket and a couple of wire nuts though.
12 AWG is rated for 41A maximum, but more importantly it is 1.588 ohms per 1,000 ft. In my case the longest run is about 60 foot total loop length so that amounts to 0.095 ohms, which equates to a voltage drop of 1.9V at 20A, which is the value of the breaker on the branch lines. 1.9V is also 38W of power dissipated in the wires. That would definitely be enough to make them slightly warm, but no more than that. As a practical matter I doubt that the DC branch lines will ever see more than 10A. My refrigerator only draws 4.3A when the compressor is running flat out. Two 40W DC electric blankets (on a different branch circuit from the refrigerator) will draw less than 7A combined.
The AC wiring from the inverter on each of the three branch circuits is 12 AWG for the most part, with some 14 AWG out near the end of the run. In this case I literally used outdoor extension chord with 3 wires, black, white, and green. The longest loop length is about 40 feet. The two breakers on the inverter are limited to 15A so these wires will never be stressed.
The single run from the generator to the battery charger is also 12 AWG with a loop length of about 35 ft. The generator is only rated at 13.3A continuous and has a front panel breaker at 20A. Shore power also feeds through that line with an unknown current limit, but the battery charger will never draw more than 11.7A and it is the only thing connected through that line.
There is a little tiny “extension chord” that runs from a water tight covered plug that is accessible from the outside of the truck to the inside of the generator bay that allows me to plug into shore power and still have my generator bay locked up tight. It is 12 AWG, only runs about a foot and has a 15A fuse in line. Whatever shore power line I might be connected to will presumably have a breaker or fuse as well, but I have no idea what current it might be so I need to protect myself.
To be continued…
|
|
|
02-06-2010, 07:14 PM
|
#154
|
Senior Member
Join Date: Apr 2006
Posts: 625
|
as far as I have been able to check....only 2 things lead to fire in a MH one being propane leaks[very common] and the other being electrical both 12 vdc and 120vac...RAN D. HAS COVERED THIS ISSUE AS IT SHOULD HAVE BEEN DONE BY THE MANUFACTURES...and as we all know the manufactures have cut corners and that is why there are electrical fires in RV's....the propane issue is easily removed from the RV with an outside grill and a grill tank and electric heaters-while the electrical is harder to work around. For our own sakes please remove the issue of propane from your RV asap....and as always, Please, if you have electrical issues ask for help from someone that knows electricity, grounding and wire sizes.....geofkaye and the Rivercity Group who looks at insurance issues of which many are easily avoidable and inexpensive to change out.....
|
|
|
02-13-2010, 10:04 PM
|
#155
|
Senior Member
Join Date: Apr 2009
Posts: 212
|
Socket to me…
Some random notes about installing the electrical, and well, sockets. Three prong sockets have got to be as common as dirt, but they are not all the same as I discovered, and not all kinds are available at every home improvement store. Mostly the seem to vary in terms of how you hook up the wires. The cheapest ones just have screws, which is fine if you have solid wires because you can just bend the wire around the screw and tighten it down. I will assume that if you are wiring an RV you are using stranded wire, and possibly many fairly fine strands at that. Wrapping those around a screw just doesn’t work.
One solution is to use crimp on lugs, and for the ground terminal, or screw, that is often the only choice. Crimp on lugs work fine if you have the right tools and know what you are doing. You can solder them after crimping if you must, but do not tin the wire and then crimp it. That will make a high resistance or unreliable joint.
Use ring lugs of the appropriate size, not fork lugs. Fork lugs have a tendency to spread and work loose, and should only be used in applications where the fork is captured to prevent spreading, like a bus bar. A ring lug can’t work loose, as it is fully trapped under the screw head. Ground screws and ring lugs are a problem though because the ground screw (often tinted green) is not meant to be fully unscrewed. They smash the last thread or two to prevent them from unscrewing and falling out. You can unscrew them though, it just takes some extra force. A good socket driver makes the job easier.
Some sockets, and switches ect. for that matter, have a plate under the screw head that pulls down on the wire. Avoid those if you can. They can work with stranded wire, but they don’t always work well. The wire strands tend to get out from under the plate and the whole thing can work loose. Pull test all your connections regardless of the socket type, just to be safe.
Some sockets have a hole in the back that you insert the wire into. They also have a screw and plate on the inside. In this case the screw pulls the plate towards the screw head and clamps down on the wire. These are the best I have found for stranded wire. They are not perfect though. Depending on the specific socket the hole for the wire can be rather small. It can be difficult to get a 12 GA stranded wire into that hole without a few strands bunching up. Truth be told, I had a few loose strands here and there that I ended up clipping off. One or two tiny strands won’t reduce the current carrying capacity much, and you don’t want them touching something that they shouldn’t be touching.
Some sockets have a hole in the back that look just like the ones you want, except that they have a spring clip arrangement that grabs the wire. They might work great for solid wire, but they are unusable for stranded wire. You have to push the wire in past the spring clip and stranded wire won’t be pushed without fraying all over the place.
GFI sockets have some similar issues, except that they are larger and leave even less room for the wire inside a small handi-box. I know of no solution except to keep the wires fairly short and then use whatever swear words you like best while putting them into the box. Just make sure you don’t pull any wires out of the socket while forcing it into the box.
Wire nuts are also a special challenge with stranded wire. By “wire nut” I mean the twist on cup like connector that has a spiral cone or spring inside. They are convenient, and they do work, but I have found that it is easy to end up with at least one wire into the nut that is not very secure. Mostly I try to avoid them by designing the wiring so that all the sockets are in a series chain. That way you can use the screw clamps that are part of the sockets to make the connections.
Sometimes you have a junction point where 3 or 4 wires come together with no socket. I try to avoid 4 wires coming together in one wire nut, and I pretty much never do 5. It is just too difficult to get all the wires twisted together with full and even contact and then get the wire nut on. Regardless of what you do, pull test everything to make sure you don’t have a wire hanging on by a strand or two. I know I found one bad connection that way. It could easily have gotten hot and started a fire.
The problem with stranded wire and wire nuts applies to the DC wiring as well. I soldered a flying lead onto some connections and then used a wire nut to make the final connection in the box. Crimp on spade lugs with the mating socket lug are another good option. My experience is that they work well, but don’t use them on a connection that you intend to connect and disconnect often. Once fully connected they can be a real bear to get apart again.
I find that crimp on lugs have marginal strain relief where the insulated wire comes out. Some of the really fancy ones have built in shrink tubing with what amounts to hot melt glue inside. They seal up really nice but are expensive and not always available at your local home improvement store. I find this is another terrific use for Goop. A little dab around the back of the crimp lug will seal the joint and dry to provide a compliant strain relief. Of course there is always regular shrink tubing as well.
To be continued….
|
|
|
02-14-2010, 04:31 PM
|
#156
|
Senior Member
Join Date: Feb 2009
Location: St. Paul, MN
Posts: 1,819
|
Quote:
wire comes out. Some of the really fancy ones have built in shrink tubing with what amounts to hot melt glue inside. They seal up really nice but are expensive and not always available at your local home improvement store. I find this is another terrific use for Goop. A little dab around the back of the crimp lug will seal the joint and dry to provide a compliant strain relief. Of course there is always regular shrink tubing as well.
To be continued….
Posts: 77 | Registered: April 03, 2009
Ignored post by Ran D. St. Clair posted February 14, 2010 01:04 AM Show Post
Powered by Social Strata Page 1 ... 13 14 15 16
Please Wait. Your request is being processed...
Logout: TruckConversion.net
Update LiveCloud Account Reply
|
The rear hole with the barb fitting is only designed to be used with 14 guage solid. They make the holes too small to push in a 12 guage.
You can wrap stranded wire around a screw teminal. The trick is this. You strip back the insulation about 1/2"-5/8". Then take that end between your thumb and finger and twist the strands counterclockwise (the opposite of the way they come from the factory). Then wrap the wire as tightly as you can around the screw (clockwise of course so when you tighten the screw it tends to pull the wire tighter around the shaft of the screw). This trick works pretty well. It was taught to me by a master electrician so I think it's legal too.
__________________
'03 Freightliner FL112, 295" wheel base, with '03 United Specialties 26' living quarters, single screw, Cat C12 430 h/p 1650 torque, Eaton 10speed , 3.42 rear axle ratio
|
|
|
02-14-2010, 09:13 PM
|
#157
|
Senior Member
Join Date: Apr 2006
Posts: 625
|
....STRIP THEM TOO LONG-TWIST THEM UP-CUT TO LENGTH AND FASTEN WITH A WIRE NUT THAT TWISTS THE WIRE ALSO...SO SIMPLE AND SO PERMANENT.....what could be easier?...geofkaye and the Rivercity Group....
|
|
|
02-16-2010, 10:40 AM
|
#158
|
Senior Member
Join Date: Apr 2009
Posts: 212
|
Back Porch Light (No it’s not a micro brew)
It might sound trivial, but I consider it rather important for my application. Sooner or later someone is going to come knocking on my back door when I am in the truck. It will probably be dark out, and it could be anything from the local cops to someone who lives there to some bad guys looking for something to steal. I need to be able to turn on my back porch light (even though I technically don’t have a back porch) and look through my peep hole to see who they are.
Alternatively, I need to be able to come up to my truck in complete darkness and fumble through my keys to gain entry. Either way, I need a light in the back, and I need to be able to turn it on or off from the outside as well as the inside.
Fortunately controlling one light with two switches is easily done. You just need two single pole double throw switches (SPDT). A SPDT switch has 3 terminals, one in the center that connects to one on each end depending on which way the switch is flipped. They are very common, both in the world of home AC wiring and in the world of electronics. The wiring schematic is often printed on the package containing the switch as you would find it in your local home improvement store. This same circuit is often used to control a central light from both ends of a room or hallway.
In my case, the back porch light is actually my left rear backup light. It is normally driven by the trucks electrical system, which in my case is separate from the house electrical system. They share a common ground, but that is all. The challenge is to have the light work as a back porch light controlled by two switches, and still work as a backup light as well. The solution is to use two diodes. This is the same technique as is often used to have a tow vehicle control the tail lights of the towed (sometimes called a “toad”) vehicle.
Each circuit drives the light through a diode. Current can go into the light from either circuit, but cannot go from the light back into either circuit. The result is sometimes called a “diode or” meaning the light will turn on if one “or” the other circuit tries to turn it on, and will only turn off when both of the driving circuits are off. It’s much harder to say with words than to draw a schematic.
I have one additional requirement. When two switches are used to control one light, you never know which position of either switch will be on or off, as it depends on the position of the other switch. This is not a problem controlling the light in a hallway as you can see the light from where you control either switch. In my case the back porch light (left backup light) is on the outside of the truck where it is not easily seen from the inside of the truck. I don’t want to accidentally leave it on and run the house batteries down. It only draws about 2 amps, so it would take a very long time to run the battery down, but still, there is no need to waste energy and burn out bulbs. I suppose I could just look out the peep hole, but it might not be night time or easy to see, so I wanted a small LED on the inside next to the switch that will light when the outside light is on.
That implies that I needed 3 wires from the inside switch to the outside switch, Two wires carry the output from the two possible inside switch positions, and one wire caries the result back from the outside switch to light my inside LED.
I ended up with a heavy duty panel mount switch mounted discretely on the back of the truck in a location where you would probably never see it unless you knew where to look. The inside switch is a standard AC wall switch of the SPDT type, mounted on the ceiling above the back door. The outside switch is mostly protected from the weather because of where it is mounted, but I also gave it a coat of Goop to help protect it from moisture. Time will tell, but it should be fine.
The schematic can be found, along with a bunch of pictures in the photo gallery under key word “Stealth”.
To be continued….
|
|
|
02-16-2010, 06:43 PM
|
#159
|
Senior Member
Join Date: Feb 2009
Location: St. Paul, MN
Posts: 1,819
|
Are you sure you need to have those diodes to prevent current from feeding back into the other circuit? You've got the light. You feed it positive current from your switch. That current lights the bulb. That current also is going to try to flow to the reverse light switch located on the transmission. It's going to dead end there since the trans will be not in reverse. If it was in reverse the light would be on anyhow. Nothing will happen to that current anyway. Now let's look the other direction. You've got the light hooked up to both your switch circuit and the transmission reverse switch. You shift into reverse and the light comes on. That positive current will also try to flow toward your switches but won't go anywhere since the switch was off. Turn the switch on while it's in reverse and no harm will come anyway. The light will be on. That's it. The current isn't going to crash into itself and explode.
I'm not sure about how you've explained the circuit for the light/switches. Each light switch isn't really a spdt. An spdt switch has a center off position and two alternate positions that current flows to either contact when you switch it to them. You can't use a spdt switch for a three way light circuit because if you leave the switch in the center position it allows no current to flow through it at all. If that were the case no matter what position you place the other switch the light will not light. A three way light switch has a common terminal and two other terminals. The current always flows through the switch from the common to either of the switched terminals. I guess that's not completely accurate since if the light isn't burning no current is flowing. But the circuit is always connected through a three way switch from that common terminal to either of the other terminals. You start with the positive wire connected to the common on the first switch. Then you have two wires running from the other two terminals on that first switch to the two switched terminals on the other 3 way switch. Then the common terminal on that second switch is wired to the positive on that light at the end of the line. I'm guessing that's the way you've got your light wired but the way you explained it kind of confused me. But maybe the way I've explained it confused you and everybody else. I've wired lots of 3 way light circuits and that's the way I understand them.
__________________
'03 Freightliner FL112, 295" wheel base, with '03 United Specialties 26' living quarters, single screw, Cat C12 430 h/p 1650 torque, Eaton 10speed , 3.42 rear axle ratio
|
|
|
02-17-2010, 07:02 PM
|
#160
|
Senior Member
Join Date: Apr 2009
Posts: 212
|
Bob, you are mostly right about the need for the diodes. The only time when they are necessary is when the back porch light is on and the truck is in reverse. As a practical matter that would almost never happen. I would have to leave the back porch light on and then be driving the truck. On second thought, I am a forgetful sort, so it could easily happen.
Without the diodes the truck starter battery would be turning the light on through the transmission switch, and the house batteries would be turning the light on via my 2 way switch as well. The net effect is that the 12V positive of the starter battery is connected to the 12V positive of the house batteries. That would be no problem if they were the same exact voltage, but they would most likely not be at the same level of charge, and if the truck were running the alternator would be charging the starter battery as well. The result could easily be a 2V difference which would drive a current limited only by the wiring resistance. The resulting current could easily be 20A or more, which would immediately blow the fuse on the trucks backup light circuit.
As for switches, there are many different kinds, and I find the terminology is often confusing. Fortunately, in this case, I am talking about one of the simplest kinds of switches. (I won’t even try to tackle some of the more unusual ones). I double checked the terminology for Single Pole Double Throw (SPDT) using Wikipidia as follows:
http://en.wikipedia.org/wiki/S...Contact_arrangements
As you can see it goes by many names. The British call it a 2-way, the Americans call it a 3-way, and it is also sometimes called a single pole changeover switch. The simplest form does not have a stable center position where neither circuit is connected, but most types do have what is called “break before make” which means that both circuits will never be connected at the same time. Some switches do have a stable center off position, and they are sometimes called Single Pole Triple Throw though I would argue that a SPTT should have 3 possible circuits, not 2. The term SPCO (Single Pole Change Over) is sometimes used to denote a center off position as well. Bottom line, when I say SPDT I am talking about a switch with only two stable positions.
I think I confused you when I referred to a SPDT switch as having 3 terminals. I was counting the “common” as one of the terminals (I was literally counting the screw lugs).
Clearly words are not the best tool to describe these things, which is why I provided a schematic. It can be found in the photo gallery under keyword “Stealth” and is, for the moment, the most recent photo posted.
By the way, your explanation of how you wire a two switch light circuit is right on. Thanks for clarifying.
__________________
|
|
|
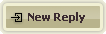 |
|
Posting Rules
|
You may not post new threads
You may not post replies
You may not post attachments
You may not edit your posts
HTML code is Off
|
|
|
|
» Recent Threads |
|
|
|
|
|
|
|
|
|
|
|
|
|