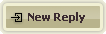 |
|
03-21-2010, 07:09 PM
|
#181
|
Senior Member
Join Date: Apr 2009
Posts: 212
|
The Walls Are Closing In On Me…
Yes, I am starting to close up the walls. Mostly that involves filling the bays between the 2 x 2 studs (actually 1 1/2” by 1 1/2”) with R-Max foam board and then putting 1/2” plywood on top. It’s mostly pretty simple, tedious and slow, but simple. I do have a few notes along the way…
My favorite tool for doing this is a long thin bladed bread knife with a scalloped edge. The long blade is best for making long straight cuts. The thin blade is good for slicing through the foam cleanly without digging out a kerf the way a saw blade would. The scalloped edge helps to keep the knife sharp and also gives it a little teeth for back and forth sawing when necessary. I don’t usually use the blade perpendicular to the material, but instead lay the handle at a shallow angle and pull it down the cut line. The first cut is only 1/4” deep, or whatever is easy. One or two slices after that finishes the job equally well for either the 1/2” or 1” thick foam. The sharp blade leaves a clean, not a crumbly edge, and it cleanly cuts the paper/foil on both sides.
Beyond that, the only other tools required are a tape measure and a Sharpee pen. The usual process is to measure the width of the stud bay, top and bottom, making note of any difference or bow in the studs. Mark out the width and make the cut in the 4’ direction across the 4’ x8’ sheet, or whatever is left of it. It doesn’t matter that a 4’ long chunk won’t fill the bay from top to bottom. In general it is a lot easier to cut and fit smaller pieces than larger ones anyway. Don’t worry if you make a little mistake, as there will be lots of scrap material to fill little gaps.
I am not using any glue, just wedging everything in nice and tight. I also fill the bays to the top, so there is no room for anything to shift or squeak. I doubt that R-Max would squeak (like Styrofoam) anyway. The usual plan is to lay the foam in 2 layers. The first layer is 1” thick and fits around all the conduit. The second layer is 1/2” thick and mostly goes over the top of the conduit, except in places where it stands proud for some reason. Mostly this only happens where conduits cross. In that case I dig out the foam on the back side of the 1/2” layer without breaking the paper/foil on the front side.
Both layers fit around all the outlet boxes. Often times you can lay the foam on top of an empty box and press it into the box a bit. This makes a dent in the foil for easy cutout of the proper shape. In some cases the conduit makes various curves and bends which the first layer of insulation matches closely. Once the boxes are clear, the foam can be smashed on top of the conduit, which makes a clear dent allowing the conduit channels to be accurately cut.
I throw almost nothing away. Even irregular pieces can be fit together to fill smaller spaces. Small pieces of foam are fairly compressible and can be cut and pressed into place. If it all fits nice and tight, it will get the job done. There is no place for air to leak anyway. The FRP (Fiberglass Reinforced Plywood) on the outer walls is inherently air tight so the insulation just needs to break up the convection loops that would allow air to move within the walls and carry heat in or out.
Of course, there are always weird shapes and buried spaces that need to be filled. When all else fails, you can use the injectible foam in a can, but I have been using very little of it. Mostly I just keep stuffing pieces of the R-Max in, back to front, top to bottom, sometimes little weird shapes piece by piece until eventually the space is filled. I am not saying it is the best method, and it may not be that time efficient, but it is what I do. If you were making a living at this, I am sure you would have to find a faster way, like spray on foam, but the R-max is what I have to work with.
I like the idea that I am creating multiple layers of foil to reflect IR (Infra Red) radiation. In some places like the ceiling there will be 4 or 5 layers, with foil between each. I can’t prove that all those layers will produce superior results, but I suspect they will.
As I cover over the conduit, I mark the conduit locations on the foam, and then lightly on the plywood. I want to keep track of where the conduit is so I don’t eventually put a screw through the wall in the wrong place.
I have designed the stud locations so that every plywood edge is supported. I am using 1 1/2” sheet rock screws every foot or so along every edge, and down every stud, along with a bead of Liquid Nails at every interface. I pre drill the holes through the plywood, but not the studs, so the screws will be able to suck the plywood down nice and tight. So tight that the screw heads are pulled well into the plywood even without any countersink. My plan is to fill these divots with non-shrink spackle later. All joints will be caulked and then spackled, but not taped. I don’t expect cracks to develop mainly because everything will be locked down so tight that it will be hard pressed to even move. (We will see though…)
Plywood is an interesting subject all by itself. It seems every home improvement store carries something different. I am using 1/2” plywood on the walls in general, and I want one good surface, but I don’t care if it has beautiful grain, or is ready to accept stain. I plan to use conventional latex semigloss after appropriate surface prep and priming. It seems the available plywood I could use ranges in thickness from .485” to 1/2” and has different surface woods. It also varies in terms of the glue used, and its rating for indoor or outdoor use. I mostly don’t care for my application, but it is amazing the lack of standardization among the different stores. You would think it would be a pretty stock item…
To be continued…
__________________
|
|
|
04-06-2010, 03:09 PM
|
#182
|
Senior Member
Join Date: Apr 2009
Posts: 212
|
The Ceiling Is Closing In On Me…
Yes, I know, I wasn’t funny the first time… Believe it or not, I am still putting R-Max in the ceiling. This has turned into a very slow and tedious task. The walls were a little slow, what with cutting the insulation to fit around all the conduit, but the ceiling is really slow. There is room for 5 each 1 inch layers of R-Max between the rafters and it takes a very long time to wedge all of those layers up there. I can literally spend all day getting just 2 bays done, and an evening after work doesn’t even complete one bay (space between two rafters). I can’t say that I am enjoying this much, so I would suggest you go talk to Geofkay about spray foam. It might not be cheaper (or perhaps it is, I really don’t know) but it has got to be faster. I would think that even two layers of fiberglass bats would be way faster, and given that I have 4 1/2 to 5 1/2 inches of insulation space in the ceiling it would probably be more than adequate. At this point I am almost done so I guess I will just stay the course. I console myself with reminders that I will have one very well insulated living space when I am done. It is already very comfortable for working on a mild winter day with nothing but the heat from my shop light.
I did end up using the injectable spray foam in a few places. I had a few small areas where I wanted to fill the space, but didn’t have much access to put the rigid foam in. I ended up wedging in some of the 1 inch thick R-Max to enclose the space, then injecting the foam in on top of it. Actually I had a whole plan, which went down hill really fast when it came time to implement. I figured I would put in about a 6 inch section of R-Max, then inject the foam in on top of it, then another 6 inch section, more foam. The plan worked great until the pressure of the expanding foam started pushing the R-Max out of place, at which point it would fall on the floor along with a big pile of wet sticky foam. At one point I was running around like a one armed paper hanger pushing the R-Max panels back into place until the foam started to act like glue and locked them into position. Needless to say, when I was done there was half as much foam on the floor as up in the ceiling. Fortunately it cleans up easily if you let it dry and harden first. Cleaning it up while wet and sticky is next to impossible.
When using the injectable foam, you have to hold the can upside down. In my case, I was injecting up into the ceiling so the little tube that comes with the can was no where near long enough. Fortunately I have some plastic tubing that is used for model airplane control linkages, so I used that. It was just the right size to press into the tube that comes with the can. It worked great. I was able to insert the tube all the way to the back of the space being filled, and then let the foam expand towards me insuring that the space was completely filled. That is, it worked great until the pressure of the foam pushed the long tube out of the short tube. When it came apart I had foam everywhere, my face, my shirt, my glasses. The can warns about not getting it on your skin, and advises wearing gloves and safety glasses, they didn’t say anything about a full body condom though. Fortunately it wasn’t that hard to get it off my face. I was so busy dealing with the rest of the mess I didn’t realize that it was all over my face until it had pretty much dried. At that point I could just pick off the rigid globs and I hardly lost any skin at all. Hey, I figure some people pay good money for a nice facial peel.
Alls well that ends well, but what I don’t know is how well the foam really filled up inside those hidden bays. I see some of the larger globs of foam that ended up on the floor tended to develop big empty bubbles inside. The whole idea of insulation is to break up the air spaces into tiny air spaces so convection loops can’t form, or at least if they do form they are really tiny. I have no idea how it really turned out, and I am not going to rip it all apart to find out. I do suspect that it will be days or even weeks before all that foam completely dries. Hopefully the fine bubble structure will last until it does. If not, oh well, it is not really a significant percentage of the overall insulated surface anyway.
To be continued….
__________________
|
|
|
04-06-2010, 07:30 PM
|
#183
|
Senior Member
Join Date: Apr 2006
Posts: 625
|
...SPRAY CAN FOAM WILL DEVELOP BIG HOLES IF NOT SHAKEN WELL ENOUGH OR IT IS TOO WARM...I KEEP IT AT 70 DEGREES IN A OLD REFER AND USE IT AS NEEDED...SPF WILL COME OUT OF THE GUN AT 135 DEGREES AND COOL OFF QUICKLY-HOLDING A SMALLER BUBBLE AND IT WILL FOAM UP ONLY SO MUCH...MUCH BETTER CONTROL THAN THE CAN STUFF....SPRAY CAN IS A CRACK FILLER AND SPF IS A INSULATOR & CAVITY FILLER....THE 2 ARE THE SAME CHEMICALLY BUT PACKAGING WILL CAUSE SOME INTERESTING ISSUES.....I GLUE IN THE BOARD FOAM WITH LIQUID NAIL AND LET DRY OVER NITE THEN SPRAY CAN IT TO SEAL THE EDGES...LET IT DRY OVER NITE AND TRIM OFF THE EXCESS.....ONLY DIFFERENCE IS THAT THE BOARD WILL ALLOW AIR TO MOVE AROUND AND THE SPF WON'T...WITH SPF THERE ISN'T AN ISSUE OF MOISTURE-WITH BOARD THEIR CAN BE A HUGE HEALTH ISSUE WITH MOLD MILDEW....1 INCH OF BOARD HERE IS ABOUT 60 CENTS AND SPF IS ABOUT $1.00 A BOARD FOOT...HEAT LOSS/CAIN IS ABOUT 40% MORE WITH BOARD AS OPPOSED TO SPF WHICH SEALS EVERYTHING TIGHT AND DRAFT PROOF....WHICH ALSO LESSENS THE ISSUE OF MOLD AND MILDEW....ALL IN ALL IF YOU ARE GOING TO KEEP THE UNITE FOR MORE THAN 3 YEARS AND HAVE ANY HEALTH PROBLEMS OR HAVE ANY ALLERGIES TO MOLD/MILDEW THEN THE ONLY WAY TO BUILD IS WITH SPF...OTHERWISE BOARD FOAM WILL DO....FIBERGLASS IS A PROBLEM WAITING FOR A PLACE TO HAPPEN...MOLD/MILDEW/AIR CONVECTION/DIRT TRAP/BACTERIA WILL GROW WITH ENOUGH MOISTURE....AND TO DRY IT OUT IS VERY EXPENSIVE....MAYBE AS MUCH AS 5 TIMES THE REPLACEMENT COST.........geofkaye and the Rivercity Girlz.....
|
|
|
04-07-2010, 11:49 AM
|
#184
|
Senior Member
Join Date: Apr 2009
Posts: 212
|
Geofkaye, Just out of curiosity, how is SPF in terms of flammability? I lit a piece of scrap R-Max on fire and it burned scary good. At least fiberglass, for all its other flaws, doesn’t burn.
|
|
|
04-08-2010, 05:48 PM
|
#185
|
Senior Member
Join Date: Apr 2006
Posts: 625
|
...THE STUFF I USE HAS A FLAME RETARDANT IN IT AND ACTS THE SAME AS WOOD-ONLY- IF THE FLAME IT TAKEN AWAY FROM THE MATERIAL-THE FIRES GOES OUT...[SELF EXTINGUISHING].KINDA LIKE THE NEW CIGARETTES THAT CAN'T STAY LIT.... PROPANE AND ANY ELECTRICAL LINES/SPARKS ARE IN CONDUIT AND OF COURSE THE PROPANE IS OUTSIDE OF THE LIVING QUARTERS-SHIELDED IN STEEL OR FLEXIBLE STAINLESS BRAIDED GAS CONDUIT/LINES. I WILL LIVE THE REST OF MY LIFE WITH THE MEMORY/NIGHTMARE OF PROPANE IN COPPER TUBING IN A TRAILER. THERE ARE JUST SOME THINGS THAT I WILL NOT TOLERATE-ONE BEING PROPANE IN COPPER LINES ON A VEHICLE. I USE A PRODUCT FOR NORTH CAROLINA FOAM INDUSTRIES AS A SUPPLIER-THE REASON THAT I USE ONLY THEIR PRODUCT IS THE FIRE ISSUE/RETARDANT ISSUE.....OTHER THAN THAT POLYISOCYNATE IS POLYISOCYNATE....THE BASE IS ALL THE SAME BUT THE ADDITIVES ARE WHAT IMPRESSES ME....ALL THREE OF MY PERSONAL HOMES AND MY T/C ARE SUPER INSULATED WITH THE NCFI MATERIALS AND I DO FEEL VERY SAFE.....SLEEPING AT NITE IS ONE OF MY FAVORITE THINGS TO DO...SPECIALLY IF THE GIRLZ ARE AROUND WITH THEIR KIDS....geofkaye and the River city Girlz......
|
|
|
04-08-2010, 05:58 PM
|
#186
|
Senior Member
Join Date: Apr 2006
Posts: 625
|
....one other issue...fiberglass will act as a substrate and will aid, to some exten,t combustion....though they only can produce the activity in a controlled situation.....it has to do with the dust load over time and installation of the material in clean cavities....something I saw as a demonstration a number of years ago.....all and all ,in a fire, it made little difference in the outcome-as the toxic smoke load of the interior of the home killed the occupants long before the flames......seems smoke is the real killer in a much shorter time......one issue here and I speak for myself.....I'm chicken chit of fire-it scares me more than anything and I go to great lengths to reduce the hazards. I want die in bed with 3 women and not in any fire/smoke/heat related accident....geofkaye and the Rivercity Girlz....
|
|
|
05-03-2010, 05:51 PM
|
#187
|
Senior Member
Join Date: Apr 2009
Posts: 212
|
Status Update 5/3/10…
It has taken what seems like forever, but the walls and ceiling are now fully closed. All the joints are caulked and all the screw holes filled with non-shrink spackle. I even have the first coat of latex primer applied. In a week or so I should have the interior painted with white semigloss latex and then it will be time to begin work on the floor.
The floor should go quickly as it is just a single layer of 1/2” R-max under the 1/2" plywood flooring. Unlike the walls, there is no conduit to work around, though there are a few holes for air vents and gas lines. That means I am getting close to installing the vinyl flooring. I am looking forward to that day as a milestone of sorts. At that point I will have a perfectly livable, but empty room. There is still a long way to go, but I can see the finish line.
|
|
|
05-03-2010, 05:57 PM
|
#188
|
Senior Member
Join Date: Feb 2009
Location: St. Paul, MN
Posts: 1,819
|
Congratulations so far. The more time you take to build it, the more you'll appreciate it when it's done. At least that's the way I justify my lengthy projects.
__________________
'03 Freightliner FL112, 295" wheel base, with '03 United Specialties 26' living quarters, single screw, Cat C12 430 h/p 1650 torque, Eaton 10speed , 3.42 rear axle ratio
|
|
|
05-04-2010, 08:39 PM
|
#189
|
Senior Member
Join Date: Apr 2009
Posts: 212
|
Details details…
I have been working steadily but haven’t been keeping up with posting the details. Some of this may be too boring to be worth reading, or obvious to anyone who is rather handy. I can’t even claim that what I did is the best way to do things. Read at your own risk.
When putting the ½” plywood up on the walls, I ended up pre-drilling and countersinking all the holes. My original plan to just let the screws pull themselves into the wood didn’t always work. Sometimes the plywood was too hard and the underlying 2x2 too soft, and the screws would just strip. Having the screw heads standing proud is unsightly and I got tired of selectively removing and countersinking stripped screws (and putting in a nearby back up screw) so I just countersunk them all.
Chip out on the plywood end grain was also an issue. My circular saw isn’t the best quality, and even with a decent carbide tipped blade it wasn’t always pretty. The wall panels are mostly 4' wide and mostly square, so I only had to cut one end. Mostly any chip out was covered by the ceiling or floor panels, but not always. Sometimes I just had to fill in the damage with non-shrink spackle. The ceiling panels have nothing to cover any chip out so spackle or caulk was the only option.
The ceiling panels were rarely perfectly square. It seems, when I put the supplemental rafters in way back when I could have measured them more carefully. It’s nothing that you can see by eye, but it is enough to force careful measurement of the plywood panels before cutting. All inside corners mate to within 1/8” or so. In some cases even “straight” edges had to be cut with a slight curve to keep to that gap. At 1/8” a bead of caulk in the corners finishes them nicely and any mistakes are well hidden.
The technique of caulking the plywood at the butt joints, and then going over the gap with non-shrink spackle mostly worked fine. The joints are almost entirely hidden except in a few places. Where I ran into trouble was due to the plywood variation in thickness. A thick spot butting up against a thin spot tends to show. Unfortunately you can’t really see all the imperfections until you have the first coat of primer in place. Differences in surface color make it hard to see differences in surface level or texture.
I cut the holes for all the outlets about 1/8” oversize. Cutting them more precisely would have required too much back and forth opening up holes that didn’t quite fit. I also have an outrageous number of electrical boxes for such a small space. I count 66 holes in the plywood for the walls and ceiling, each one carefully measured and then transferred to the plywood panel by hand. Frankly, I was surprised I didn’t loose any panels by cutting holes in the wrong places.
Once the walls were in I realized that I had a few electrical boxes that were standing slightly proud. They are all plastic, so a quick pass with the router brought them down to flush.
I eventually caulked all the gaps between the holes and the outlet boxes. I probably didn’t accomplish anything useful by doing so. The walls are full of foam that fits tightly to the boxes and the back side of the plywood so It’s not an issue with air infiltration or anything. Mostly it’s just me being fusbudgety, but that’s how I roll…
The air conditioner is recessed into the ceiling and the ceiling opening around it is a special case. I wanted broadly beveled edges and rounded corners to allow the air coming out to flow smoothly and stick to the ceiling. That required a router with a rounding bit and a temporary fence. The broad bevel was created with more non-shrink spackle. It isn’t structural, but I think it is tough enough if you coat it with a couple of layers of glue and then paint. I like to use Titebond II as a surface hardener in cases like this. I also use it to toughen up and seal exposed plywood edges. It is reasonably water proof, so I don’t worry about light moisture exposure due to condensation. I wouldn’t recommend it for something that is constantly wet though.
I put a coat of latex primer on the walls and ceiling. I suppose I could have gone directly with interior latex paint but I wanted a reasonable surface for the finished coat. The grain on the raw plywood tends to raise up when painted with a water based paint, and it does so with the primer as well, but at least I can knock it down with a sanding block before applying the finish coat.
I don’t recommend sanding regular latex paint. The surface rips and tears under the sanding block making little gummy balls of latex paint. Instead of knocking down the high spots it makes frayed edges that show through the finish coat. Regular home construction techniques would texture the walls to hide minor imperfections, and then use flat latex paint to further hide them. I wanted a smooth semigloss finish, so I probably just made more work for myself, but there is nothing unusual about that.
I am not sure if this is stupid or not, but I have been doing all the painting with a brush. I was telling myself that the primer coat needed to be worked into the wood, but that’s probably nonsense. There are lots of things to paint around but a roller would probably be faster. A roller would leave a bit of a texture, which would probably be OK as well. I haven’t actually done all that much house painting in my life so some of you could probably recommend a better technique.
I installed one of my overhead lights made from Christmas tree lights. I noticed that some of the LED’s were blinking, and then I realized that some of them weren’t even lit. I don’t know what is going on, but those LED’s just aren’t reliable. Reluctantly, I tossed them and replaced them with a standard 12V florescent light.
One of the overhead LED lights I made was built inside the plastic housing of an overhead florescent light that came with the truck but was dead. I found that the plastic housing trapped the heat from the LED’s and even though it only draws a couple of amps, it was getting quite warm inside. It doesn’t help that the ceiling pockets where the lamps reside are surrounded by R-max giving nowhere for the heat to go.
The florescent lights that I bought have an aluminum housing which helps to carry the heat down to the external surface where it can radiate away. They get warm, but only warm. They are also a bit brighter and produce a warmer light. They draw a little more current than the LED’s but not much. I still think LED’s are a good idea, but my implementation sucked.
It’s like I keep telling the guy who is paying for all of this. If you wanted perfection you should have hired someone who knew what they were doing…
To be continued…
|
|
|
05-05-2010, 07:32 AM
|
#190
|
Senior Member
Join Date: Feb 2009
Location: St. Paul, MN
Posts: 1,819
|
Too late now, but maybe for later. I've seen lots of automotive type bulbs coming out in l.e.d. For ceiling lighting I bet a guy could find a utility type light housing, like the backup lights on a truck or something, and put in an l.e.d. bulb? Or, now I'm even seeing those 4" round grommet mount backup lights in l.e.d's, wouldn't something like that work for a ceiling light? Does a 36 l.e.d. fixture use less wattage than say a flourescent fixture?
__________________
'03 Freightliner FL112, 295" wheel base, with '03 United Specialties 26' living quarters, single screw, Cat C12 430 h/p 1650 torque, Eaton 10speed , 3.42 rear axle ratio
|
|
|
05-05-2010, 05:57 PM
|
#191
|
Senior Member
Join Date: Apr 2009
Posts: 212
|
Bob,
I would guess that a properly designed LED fixture would use about half the power for the same amount of light as compared to a descent florescent light. Both are way better than incandescent. Don't take my estimate as hard data though. I figure if the LED light manufacturers ever really focus on making light efficiently then they will beat florescents by a wide margin. For now they seem to be focused on making LED's brighter and the overall fixtures cheaper. That's all well and good because it is what the market seems to want, for now, but eventually as energy prices rise efficiently will command a price premium.
I should mention that Geofkey gave a ton of good LED lighting options back on page 10. I haven't even scratched the surface on the research he did.
|
|
|
05-05-2010, 06:00 PM
|
#192
|
Senior Member
Join Date: Apr 2009
Posts: 212
|
More Details…
I wanted to quiet down my generator a bit, and possibly also provide insulation between the generator bay, under the truck, and the living quarters. I blocked up the openings between the metal floor joists and drilled some holes through the wooden floor above the generator bay. I then injected foam to try and fill the space. This time I used a canned foam that is intended to seal around windows and doors. They claim it will not bow the door frames, and that it remains somewhat flexible for life. I sprayed some water in through the holes just to make sure it was good and moist in there before injecting the foam. Unfortunately in these hidden applications I have no way to know how well I filled the space. When foam starts oozing out of the cracks I figure it is full, but I don’t really know.
I also don’t know if it really quieted anything down. I realized later that much of the noise was coming up through an open air vent related to the toilet. It sits about 4’ from the generator exhaust and was projecting sound directly into the interior. With nothing but hard walls inside (for now) the noise bounces around pretty good. That vent provides for combustion air to the toilet, and will eventually be covered by the toilet. I would be worried about hot exhaust gasses from the generator entering the living quarters but the toilet itself is mostly sealed, from the inlet vent all the way to the exhaust flue. Of course if I open the toilet lid it isn’t sealed and any seal is never going to be perfect anyway.
It remains an issue of concern, which is why I will be installing a Carbon Monoxide detector. With so many things in such a small place it is difficult to insure that exhaust fumes don’t find their way back in somewhere. I know that some RV’s have a generator exhaust that extends up well over the roof line, and I think that would be a fine solution, but it doesn’t work very well with the small portable generator I am using, (Honda Eu2000i).
Depending on where I am camping, I may be able to remove the generator from the generator bay and chain it to a tree or something. That would reduce the noise and the fumes. As a stealth camper, I need to be able to operate in an urban setting as well, so I also need to be able to charge batteries when the generator is on board. I can do that, but I will have to put up with the noise.
The Honda generators are relatively quiet, but the total perceived noise inside the living quarters relates to many factors. I am not saying that it is really loud or anything, but it could be better. The air conditioner (a standard Coleman Polar Cub roof top unit) is also a bit loud. I thought all the ceiling insulation would quiet it down a bit (and it probably did) but it is still a bit loud. For the moment it comes back to having an empty room with hard walls. Once I have bedding, curtains, and other soft surfaces it may calm down. Fortunately I don’t personally mind a bit of white noise. It tends to mask the more startling sounds that wake me up or otherwise annoy me.
I have been using my batteries and inverter on a regular basis while building the truck. All the tools, lights, vacuum cleaner, etc. that I have been using are running off the inverter with no problems so far. I just plug the truck in via extension chord to the battery charger and put the energy back in as fast as the inverter takes it out.
I did notice that the air inside by inverter bay was getting nice and warm though. That bothers me, because it has been mostly cool outside, and I went to a lot of trouble to make sure I had good airflow through the inverter bay. Once it gets hot out, or even really hot out, like 105F in the California dessert, and I am running the generator, battery charger, air conditioner and Inverter all at the same time, I don’t want to see much temperature rise between the inside of the inverter bay and the outside air.
After looking at the situation, I think I know what the problem is. I designed the battery charger and inverter to use their internal fans to draw fresh air into the bay, and then push the hot air out through a separate opening. The air path is sealed so the hot air can’t circulate back around to the input side within the bay. What I didn’t consider was that the battery charger might be running hard while the inverter was loafing (or the other way around). Both the battery charger and inverter have fans that run hard or not at all depending on how hot they are. I think what is (was) happening is that the battery charger was running full tilt but the inverter was doing almost nothing. The hot air would exit the battery charger and then sneak backwards through the inverter, then loop back through the battery charger again (not good).
To fix the problem I added an air baffle between the battery charger and inverter. Now the exhaust air from the battery charger (or the inverter) has no choice but to go straight outside. Once outside it could try to sneak back in through the inverter exhaust filter, but hopefully once in the open air outside it will mostly blow away and dissipate. Also, in order to sneak back in, it would have to overcome the resistance of the exhaust filter, which isn’t much, but hopefully helps to reduce the backflow. When air exits the bay it has to come in somewhere else, which is intended to be through the filtered inlet, which is physically a few feet from the outlet. Hopefully it won’t loop back that way, at least not much. If I have to I will add a temperature controlled fan to the inlet air vent and force the issue. I would rather keep things simple though.
As soon as I get a really hot day this summer I will have to run a full test with the air conditioner, generator, and everything else running all day long. I am sure my neighbors will love that. They are already bitching about me making too much noise with my table saw in the garage. I guess I can try to park the truck down the block while I run the test. It’s important not to piss of your neighbors because they know where you live….
To be continued….
|
|
|
05-06-2010, 05:49 PM
|
#193
|
Senior Member
Join Date: Feb 2009
Location: St. Paul, MN
Posts: 1,819
|
I would bet the inverter has a temperature shut down if it gets too hot. So I wouldn't worry about it too much unless it shuts down on you. Maybe you should put a high temp alarm sensor in the bay and hook up a buzzer or something inside so it alerts you if it's getting too hot in there?
__________________
'03 Freightliner FL112, 295" wheel base, with '03 United Specialties 26' living quarters, single screw, Cat C12 430 h/p 1650 torque, Eaton 10speed , 3.42 rear axle ratio
|
|
|
05-11-2010, 07:56 PM
|
#194
|
Senior Member
Join Date: Apr 2009
Posts: 212
|
Bob,
You are correct. It will shut itself down if it gets too hot, and it already has a built in buzzer. I have managed to make it go off a few times by charging the battery and then turning off the AC load. I assume the inverter was alarming due to battery overvoltage. Even if the overvoltage was only for a few milliseconds, it won't shut up until I power cycle the inverter.
Back to the heat issue... Heat kills electronics. The rule of thumb is that the service life is cut in half for every 10 degrees centigrade temperature rise. Even if it doesn't overheat enough to turn itself off, running hot isn't good for it. My baffle seems to be working, though I don't have hard data to prove it.
|
|
|
05-11-2010, 08:02 PM
|
#195
|
Senior Member
Join Date: Apr 2009
Posts: 212
|
Still more details…
My truck is oozing. Yes, I’ts pooping foam out the back. You may recall I used the canned foam in a few small areas in the ceiling where I couldn’t get access to put in the R-max. That may have been a bad idea. It’s over two weeks later and the foam is still liquid inside there and trying to find a way out. It pushed its way out of a few tiny seams in the outer metal shell on the back of the box, above the rear doors. Once the foam gets out it hardens and can be easily removed, but then it starts oozing again. I figure that eventually it will dry out in there but it may take weeks or even months. For now I am just going to live with a few growths on the back of my truck. Scraping them off sometimes takes the paint with it, so I might as well let it finish before messing with it again.
Oh, and here’s another odd end… About a year ago when I first got the truck, I got tagged in my driveway. A plain white truck just sitting there was too much temptation for the local idiots I guess. Fortunately the FRP (Fiberglass Reinforced Plywood) is pretty much immune to any normal solvents, so I was able to clean it off with lacquer thinner and some paper towels. The painted metal areas of the box (of which there aren’t much) were not so easy as the lacquer thinner attacks the truck paint. Mind you, I am not talking about the automotive paint that is used on the cab. It seems to be made of sterner stuff. The white paint on the metal parts of the box is more like rattle can paint, while the paint on the cab is catalyzed automotive paint with a clear cote, entirely different.
I decided to protect my truck and I read somewhere on this forum that floor wax works well. (I think it was in a post by Geofkey.) I went to the hardware store, K-mart, etc. looking for floor wax, but it seems like no one sells it any more. I assume you can still get it from an industrial supply or similar, but I didn’t want 5 gallons of it or anything.
I did find a floor “Sealer Wax” and reading the label It appears to be more of an acrylic than a wax. The stuff I used is called TREWAX Gold Label Sealer Wax and I got it at the local hardware store.
I will tell you right now that it doesn’t work as a spray paint barrier (I tested it). The spray paint sticks to it well enough, and it is just as hard to remove the spray paint with lacquer thinner from atop the sealant as it was from the FRP itself, harder actually because the lacquer thinner dissolves the sealant as well and loads up the paper towel. I would mention it no more, except that it seems to make the perfect no buff car wax.
Now I am not suggesting that you put this stuff on your prized show car, but hear me out. I put it on my beater car and my truck a year ago and it is still there and still shiny. It makes everything shiny, even the flat black bumper on the back of my truck, rubber hoses, plastic, etc. Dull oxidized aluminum looks nice and shiny with just the wipe of a sponge. Basically, if you don’t want it shiny, then don’t put this stuff on it.
It is super easy to apply. Just wash the car really well. It had better be clean because any dirt or smudges will be sealed in. Apply the stuff with a damp sponge. One wipe on and you are done. I used one of those sponges with a micro-fiber cover, also from the hardware store. It’s more like painting with a water based clear cote than waxing. It self levels nicely, goes on crystal clear and doesn’t yellow over time. That’s why I waited a year to tell you this. I wanted to make sure nothing ugly was going to happen.
I put it on my 92 Geo Storm that has some peeling clear cote on the fenders. (Don’t even get me started about the idiot mechanics who put it under a lift with another car leaking break fluid.) It sealed down the clear cote edges and made them almost disappear. Once the edges were sealed it stopped further peeling, which was only getting worse. It’s still a beater car, but now I can at least wash it and get it clean.
Use it or not at your own risk. I have no idea whether it provides any kind of a UV shield to protect the paint in that way. I also don’t know how to safely remove it. Lacquer thinner works, but I wouldn’t call that safe removal from a car finish. For my purposes it is the perfect car wax though. Easy to apply and looks great. For things with less than perfect paint to begin with, I think its ideal, and not even expensive.
To be continued…
|
|
|
05-12-2010, 07:40 PM
|
#196
|
Senior Member
Join Date: Apr 2009
Posts: 212
|
Perplexing Power Plugs…
AC plugs and sockets are easy. They have been standardized for many years. There is no question what you should use and they are readily available. 12V DC sockets and plugs are another matter. The only real standard that I know of is the ancient cigarette lighter socket. It’s bulky, and electrically speaking, not a very good connector though.
I had planned on putting 5 DC plugs in my truck. The only ones I had any specific plans for were in the sleeping area, so I could plug in a DC electric blanket. The others are in the kitchen, or in the computer area just in case. I have some Lithium Polymer battery chargers that run off of 12V for example.
I mounted some cigarette lighter sockets in blank electrical outlet covers but I was never really happy with the result. It almost worked, but the sockets are so deep that they pressed up against the back of the handy-box and in some cases bowed out the cover. It was also very difficult to get all the wires and wire nuts back into the handy-box because that big fat connector takes up so much space.
I finally got fed up and decided to at least look for an alternative. I had a bunch of Anderson Powerpole connectors in my junk box from a project years ago, but they are designed as an in-line cable connector, not a bulkhead mount connector. I threw some in my pocket and started browsing the local home improvement store (Lowes) and found an electrical box cover with a square opening intended for modular data and phone connectors. It just happens to be a perfect fit for the Anderson Powerpole connectors in a 2 by 2 array. I slightly filed the opening to bevel the front side for easier plug insertion but that was it.
I just soldered the wires into the contacts, or in my case soldered the wires to the wire stubs left over from the previous project, shoved the connectors into the mounting plate, and gave the whole thing a good coating of Goop. I love Goop. It’s sort of the duct tape of adhesives. It sticks to almost anything, including smooth plastic, remains a bit flexible forever, and can be peeled off if you ever really need to.
The downside is that when I buy 12V electrical appliances, I will have to cut off the cigarette lighter plug and solder on the mating Powerpole connectors. The upside is that I will have real connectors that are up to the task of carrying up to 30A without falling out or making intermittent contact. I can also plug in up to 2 appliances per outlet, where before I could only plug in one.
If you are not familiar with Powerpole connectors, here is a link:
http://www.mcmelectronics.com/...0&CAWELAID=220239965
They are not cheap, but not overly expensive either. The individual connectors are sexless, meaning you can plug any connector into any other connector. The little plastic housings have dovetail keys that allow you to lock them together. When you do that you can create a polarized “plug” and mating “socket” without any possibility of a reverse polarity connection, because they simply won’t fit. The housings come in red and black which is also a handy visual reference for polarity.
The contacts are almost fully enclosed in the plastic housings, making it difficult to touch them, and while it is not as critical for 12V as it is for 120V it’s still a nice safety feature. The contact area has a heavy silver plating which gives them their excellent electrical properties. They have a nice “over center friction lock feel” on engagement so they don’t just fall out, but they also don’t hang on so aggressively that you can’t get them out without ripping your fingers off.
In a world where cheap is the definition of good, they will probably never become an industry standard, but they have just become my standard. As always I have provided pictures that can be viewed under keyword “Stealth”.
To be continued…
|
|
|
05-12-2010, 09:06 PM
|
#197
|
Senior Member
Join Date: Feb 2006
Location: OKC, Ok.
Posts: 109
|
Just a suggestion,...why don't you leave the 12V cig lighter recepticles & just add the Anderson Power Pole plugs to the same box.
Then you will be able to power up just about any 12V accessory that comes along.
If you are having a problem with the length of the cig recepticles, You might look at these:
http://cgi.ebay.com/ebaymotors...5fAccessoriesQ5fGear
http://cgi.ebay.com/ebaymotors...fPartsQ5fAccessories
There are also several others available,...I found some (short) surface mount recepticles at a swap meet a while back that are water resistant & have mounted a couple on my motorcycle for the GPS & heated vest etc,...
|
|
|
05-13-2010, 07:26 AM
|
#198
|
Senior Member
Join Date: Apr 2009
Posts: 212
|
Bob, Those are both great options. If I had known about them I probably would have gone with the dual socket plate. For now, I have made my bed and will sleep in it, but I think you have done a great service for future readers.
|
|
|
05-14-2010, 06:32 PM
|
#199
|
Senior Member
Join Date: Apr 2009
Posts: 212
|
Status Update
I completed the painting of the walls and ceiling. It took one coat of primer and two coats of white latex semigloss before I was satisfied with the coverage. The fact that it took 3 coats surprised me as I was painting over clean new plywood which is a fairly light color to begin with. I decided to go ahead and use a texture. Drips, runs, and brush marks count as a texture right? Seriously, it’s not that bad, but it’s not perfect either. A year from now it will all be forgotten but for now every little mistake haunts me.
I am not sure that I can share any great wisdom about brush painting latex, but I can share one thing. If you just brush it on and walk away, you will have sags and runs. If you brush it on and then keep working the brush back and forth until it starts to drag the brush down, like you are brushing on glue instead of paint, it won’t run. Better yet, brush it on one way, and then dry brush it the other (like vertical and horizontal for example) and most of the brush marks will cancel out. I welcome anyone who is a serious painter to jump in and straighten me out on this….
I started putting on the electrical outlets and covers, which takes a surprisingly long time since there are so many of them. I found that the plywood gaps around the boxes are ever so slightly too large to be covered in some cases. I could use oversize covers, which they sell in two larger sizes, but I want to use the small, or standard size. Almost all my outlets and covers will be between shelves in what amounts to permanently mounted book case style cabinets and I don’t want them bumping into the shelves or the vertical supports. I will just have to add a little caulk around the edges of the boxes to fill any gaps. In truth, I could just ignore it, but I am just nitpicky like that.
I am also a little unhappy with a few of the AC plugs. It another fusbugety thing, but a few sit just a little too deep and will need to be shimmed out. I don’t like the way they distort the unbreakable plastic outlet cover plates so I will just have to fix them.
All the ceiling lights, fan, air conditioner etc. are installed. I still need to install the hand cranks and the pointing handles for the two antennas. I also need to install the WIFI amplifier and cover plate for the broadcast TV amplifier box. If everything fits as planned it’s just a matter of a few screws and possibly a lick of paint here and there.
I installed the wired remote for the inverter. It also has a wireless remote which I believe communicates with the wired remote. The bottom line is that I can now turn the inverter on/off from inside the living quarters. It’s handy for now, but in the long term it will probably be left on 24/7. Then again, I may get in the habit of turning it off at night to conserve battery power. Then again, again, it doesn’t draw much when idling, and I have a ton of batteries.
I installed the plywood floor on top of ½” of R-max as planned. The next step is to fill in the gaps and seams to prepare the floor for vinyl flooring. That will probably happen this weekend.
I will need to special order the vinyl flooring. I didn’t realize how expensive that stuff can be. Sure, you can buy the cheap stuff for a buck or two per square foot, but I haven’t been cutting corners on materials to this point. Also, the cheap stuff looks like every crappy little apartment I have ever lived in and I just can’t stand to look at it. The good stuff is almost $4 per square foot. At 14’ by 7’ I have 98 square feet, but that’s irrelevant. It comes in 6’ wide or 12’ wide rolls, so I will need to buy 14’ by 12’ and that is 168 square feet, or about $672 plus tax. I may look around for a better deal, but will probably just spend the money and keep moving forward. In the big picture it is not that much, and this is planned to be my one and final home for the rest of my life, so I don’t want to regret the $100 I saved.
To be continued…
|
|
|
05-14-2010, 06:49 PM
|
#200
|
Senior Member
Join Date: Feb 2009
Location: St. Paul, MN
Posts: 1,819
|
I thought the a/c recepticles should not depend on the box sitting flush with the face of the plywood. The ears (metal tabs above and below where the mounting screws go through the device) are made to sit on the face of the wall. You only tighten them into the box far enough to get those ears sitting on the face. Then put the cover on. If your plywood is cut too big around the box (like you said a few are) I think you can place spacers over the mounting screws so that the device will tighten to the box and be the right depth for the cover plate to attach and sit right on the wall surface. Seems to me I remember seeing these spacers in the electrical tidbits isle at Menards/Home Depot?
__________________
__________________
'03 Freightliner FL112, 295" wheel base, with '03 United Specialties 26' living quarters, single screw, Cat C12 430 h/p 1650 torque, Eaton 10speed , 3.42 rear axle ratio
|
|
|
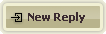 |
|
Posting Rules
|
You may not post new threads
You may not post replies
You may not post attachments
You may not edit your posts
HTML code is Off
|
|
|
|
» Recent Threads |
|
|
|
|
|
|
|
|
|
|
|
|
|